Пожалуй, больше всего в девяностых пострадало машиностроение, не выдержавшее конкуренции с зарубежной продукцией. Многие заводы закрылись. Выжившим российским компаниям пришлось учиться новым подходам к бизнесу. Одно из решений нашлось в Японии. Олег Дерипаска привез в Россию производственную систему компании «Тойота» и адаптировал ее под потребности российских производств. Как идеи Страны восходящего солнца позволили возродить легендарный Ярославский моторный завод – в нашем материале.
Своевременные комплексные перемены
Основанный в 1916 году завод «Автодизель» вступил в XXI век с серьезными проблемами. Спад производства 90-х, забастовки, бартер, отсутствие инвестиций, устарели принципы работы.
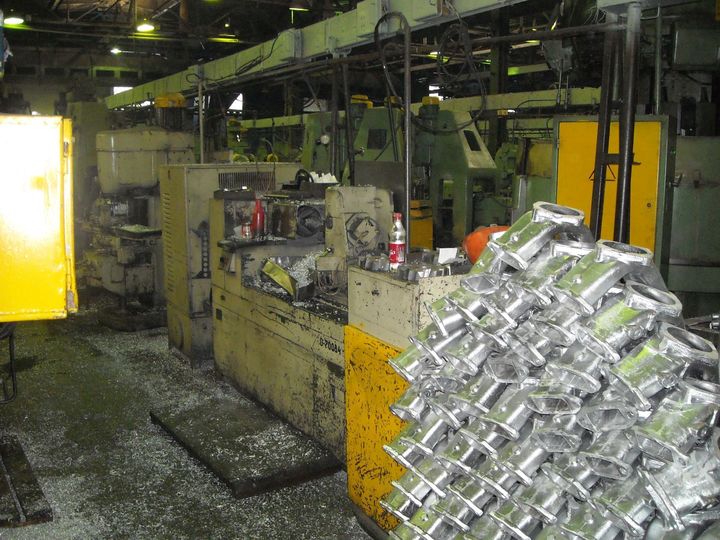
В 2001 году собственником предприятия стала компания «Руспромавто», впоследствии «Группа ГАЗ». Случилось это в то время, когда заводу нужны были свежие идеи и решения. Основным идеологом новой жизни ЯМЗа стал главный акционер предприятия Олег Дерипаска.
Чему Ярославский моторный завод научился у «Тойоты»
Перемены на ЯМЗ пришли из Страны восходящего солнца.
«Главный акционер Олег Владимирович Дерипаска был в Японии, на «Тойоте», – рассказывает директор по производственной системе Ярославского моторного завода Александр Гусаров. – Его впечатлил подход к организации производственных процессов. Он понял, что эффективность этой системы очень высока, и решил воспроизвести подобное в России».
Первые шаги по внедрению японской системы были сделаны на нижегородском ГАЗе – ключевом предприятии «Группы ГАЗ». На завод была приглашена японская консалтинговая компания. Затем специалисты Нижнего Новгорода стали живым примером для ярославцев.
«По поручению акционера руководство ГАЗа очень много сделало, чтобы система начала внедряться у нас, – делится воспоминаниями начальник отдела планирования производства Ярославского моторного завода Андрей Завьялов. – Нижегородцы приезжали, учили нас, давали задания, а потом возвращались и смотрели, как мы справились».
Ярославцы ездили в Нижний Новгород учиться у коллег.
На предприятии началось время глобальных перемен для всех: от генерального директора до рабочего цеха.
Ожесточенная борьба с потерями
«Автодизель» менялся на глазах. То, что произошло, стало настоящей революцией – вспоминают сотрудники предприятия. Менялось все – даже место общезаводской планерки.
«С началом внедрения производственной системы в 2004 году мы стали собираться прямо у сборочного конвейера. И там на производственной площадке всем участникам совещания было видно: есть ли некомплектные моторы, по какой причине, какие проблемы возникают на рабочих местах. Все самое важное происходит именно на производственной площадке, гембе», – рассказывает директор по операционной деятельности Ярославского моторного завода Константин Назаров.
С японского языка «гемба» можно перевести как «место событий», а применительно к производственной системе – место создания продукта. Принцип гембы: решать проблемы на производстве, в цехах.
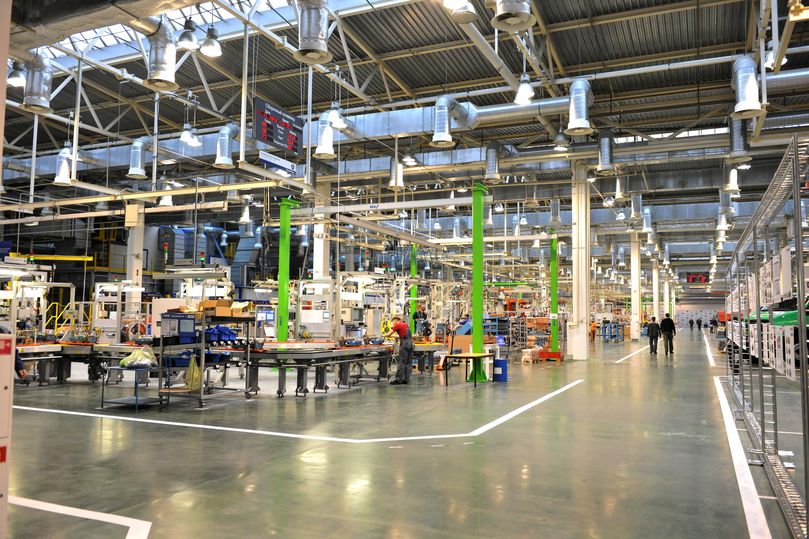
На ЯМЗ начали с выявления потерь. Вычислялась любая работа, которая не добавляет продукту ценность.
Бессистемные запасы сменило планирование. Были разработаны стандарты выполнения операций, от техники безопасности до расстановки станков.
Для разработки стандартов создавались межфункциональные рабочие группы. Люди учились смотреть по-новому на свою работу и работу коллег. И прежде всего смотреть критически. Искать недостатки, которые мешают движению вперед. Но не для того, чтобы наказать кого-то, а для того, чтобы понимать, что нужно исправлять. Операции стали замерять по времени. На рабочих местах появились специалисты с секундомерами.
«Мы провели хронометраж рабочего времени, изучили все операции и нашли возможность увеличить производительность труда здесь на 40%», – рассказывает директор по операционной деятельности Константин Назаров.
Процесс пошел. Работа по выявлению и подсчету потерь на производстве была поставлена на конвейер. Но главная задача состояла в том, чтобы изменить мышление сотрудников, многие из которых сперва принимали нововведения в штыки.
Отказ от запасов и ориентир на заказчика
Старожилы завода с советскими принципами сперва с недоумением воспринимали новые японские термины, а также значительные изменения на производстве.
«Раньше люди были сосредоточены на выполнении плана и на остальные проблемы практически не обращали внимания», – рассказывает начальник кузнечно-прессового цеха ЯМЗ Александр Скрылев.
Наиболее тяжело воспринимался отказ от запасов, вспоминают сотрудники «Автодизеля».
«Работники не ожидали такого неординарного подхода. Это наше «а вдруг пригодится?» было перечеркнуто», – вспоминает начальник литейного цеха Александр Гусаров.
Японский подход заставил по-новому взглянуть на привычные вещи. И тут уже трудно было не заметить, что «как привыкли» не всегда означает «хорошо». Начиналось все с, казалось бы, банальных моментов.
«У нас на сборочном конвейере находился склад топливной аппаратуры, – вспоминает Андрей Завьялов. – Рабочий должен был прийти на склад, взять насос, положить на тележку и привезти к конвейеру. Эти манипуляции занимали много времени. Мы взяли стеллажи, на которых стояли насосы, перенесли к конвейеру. И сократили путь рабочего на 15–20 метров».
На первый взгляд, небольшое расстояние выливалось в дни напрасно потраченного времени, которое в итоге оплачивал потребитель конечной продукции.
«Раньше в кузнечно-прессовом цехе люди переносили детали вручную. Чтобы облегчить труд, мы внедрили рольганги – рамы с роликами, по которым детали перемещаются от станка к станку. Операторы оценили этот кайдзен и стали просить еще», – рассказывает начальник кузнечно-прессового цеха Александр Скрылев.
Когда рабочий видел, что его труд становился легче и производительнее, то уже охотно соглашался, что новшество – необходимость.
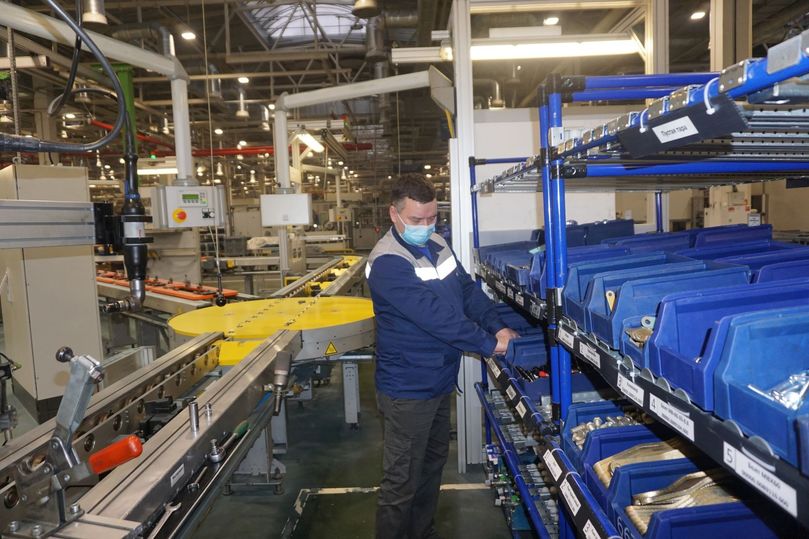
Топ-менеджмент в деле
Руководители «Автодизеля» доказывали положительное влияние новой производственной системы личным примером.
«Высшее руководство завода курировало внедрение инструментов производственной системы в цехах. Начальники подразделений докладывали о проделанных улучшениях, в разговоре обязательно принимали участие рабочие. Руководство интересовалось – удобнее ли вам стало работать? Порой звучали и замечания. Люди вовлекались в эту работу, вступали в открытый диалог с топ-менеджерами. Получался союз администрации и представителей производства», – говорит Андрей Завьялов.
Перестраивалась система взаимоотношений внутри предприятия, которое теперь стало ориентироваться на заказчика. При этом заказчиком понимается не только конечный потребитель продукта, но и соседний цех, для которого производится деталь, или сборочный конвейер.
«Раньше, если одно подразделение имело проблему с другим, то передавало информацию о ней наверх – высшему руководству. Вопрос шел до верха, а потом снова спускался вниз, – рассуждает директор по производственной системе Александр Гусаров. – Производственная система научила людей работать на горизонтальных связях, на своем уровне: начальник участка решал вопрос с начальником участка, заместитель – с заместителем и так далее».
Сотрудники получили больше самостоятельности и полномочий. А это также потребовало иного образа мышления. В коллективе стали появляться активные сотрудники, предлагающие новые улучшения.
Движущая сила производственной системы ЯМЗ
«Люди – самый ценный актив». Так звучит один из постулатов производственной системы «Группы ГАЗ».
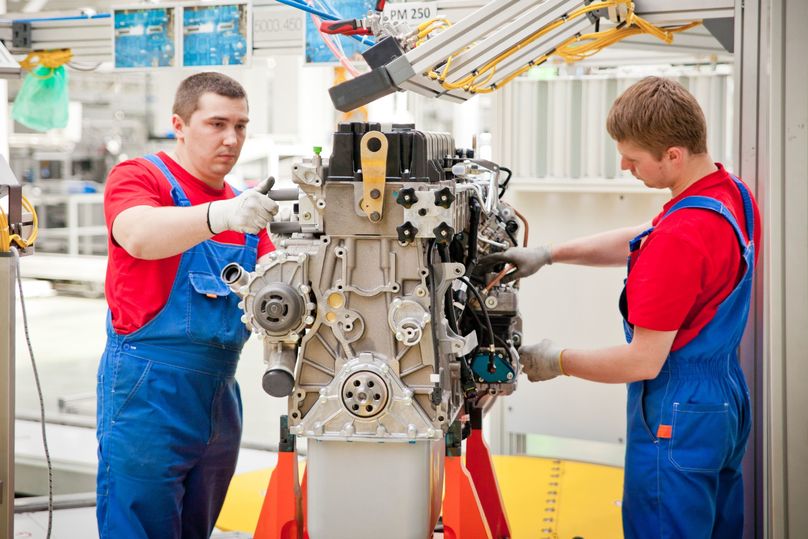
Рабочий компании – это больше не винтик системы, а самостоятельная единица. Если возникает проблема, которая не решается быстро, любой сотрудник может дойти до директора. Более того – он обязан это сделать.
«Информация о цепочках помощи вывешена на стенах. Если, например, сломался инструмент, нужно позвонить такому-то человеку», – объясняет главный специалист по производственной системе ЯМЗ Дмитрий Шеполухин.
Способов работы с людьми немало. Стандартизация рабочего места, понятные инструкции, техника безопасности, режим труда и отдыха, удобная спецодежда и система мотивации. Например, соревнования между подразделениями.
«У нас есть заводская доска почета, цеховая доска, льготные путевки в санатории. В первую очередь рассматриваются работники, к которым нет претензий по работе и кто ответственно и инициативно относится к своему делу», – рассказывает начальник кузнечно-прессового цеха ЯМЗ Александр Скрылёв.
Материальное поощрение получают авторы «кайдзенов» – производственных улучшений. В каждом цехе есть техническая комиссия. Она рассматривает предложения сотрудников. Если идея будет оценена как полезная, она тут же принимается к исполнению. Усовершенствования поставлены на поток, что дает работникам серьезную мотивацию.
Перемены по всем фронтам
Изменился маркетинг, подход к прибыли. Согласно философии системы, прибыль – это цена, по которой продукт готов купить покупатель, минус затраты на производство. Постоянная работа над затратами повышает эффективность производства.
«Когда мы входили на конвейер средних грузовиков на «ГАЗе» с мотором ЯМЗ-530, двигатель имел ряд издержек, мы продавали его практически с нулевой маржой, – говорит директор по развитию Ярославского моторного завода Николай Шамаль. – Но благодаря внедрению инструментов производственной системы и серьезной работе с поставщиками мы добились маржи и конкурентоспособной цены».
На предприятии пристально следят как за конкурентами, так и за тем, как работают двигатели, вышедшие из цехов «Автодизеля».
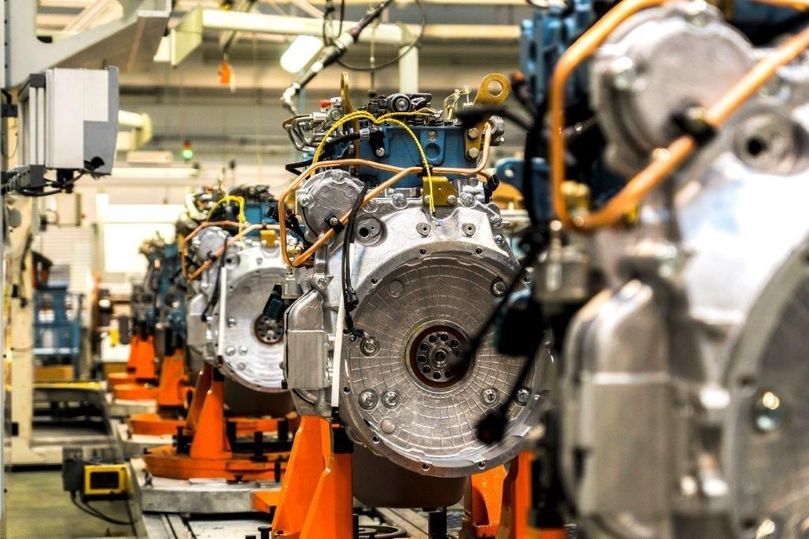
«У нас постоянно проводится анкетирование клиентов, и по результатам измеряется их удовлетворенность. Также мы опрашиваем клиентов, которые продают запчасти на вторичный рынок и станции технического обслуживания», – рассказывает директор по качеству Сергей Вальков.
Важным направлением стало отношение к качеству. Сегодня производственные процессы на предприятии сертифицированы по международным стандартам ISO-9001 и IATF 16949. Стандарт IATF 16949 разработан специально для поставщиков автокомпонентов. Сертификация подтверждает работу «Автодизеля» на уровне ведущих мировых компаний.
«Мы прекрасно понимаем, что потери по качеству серьезно влияют на финансовый результат предприятия. А в итоге на возможность поощрять сотрудников и получать ресурсы для инвестиций. Качество – это приоритет», – говорит Сергей Вальков.
Подходы ЯМЗ оценили зарубежные коллеги из Daimler. В Ярославле несколько лет собирались двигатели для фургонов «Мерседес». Три года назад «Автодизель» получил премию «Quality Award» от Daimler за достижения в области качества производства двигателя для Mercedes-Benz Sprinter Classic.
Регулярное развитие по-японски: кайдзен каждый день
Японская система позволяет решить российскую проблему непостоянства. На стабильное развитие настраивает кайдзен – система непрерывных улучшений. Принцип создает культуру производства, которая побуждает к регулярным улучшениям на каждом рабочем месте.
«Поговорка «нет предела совершенству» обрела новый смысл. Улучшение, поиск потерь, их устранение и снова в бой», – улыбается директор по операционной деятельности ЯМЗ Константин Назаров.
Постоянные улучшения измеряются в рублях. Эффект кайдзена подсчитывается ежегодно.
«Мы считаем эффект по всем мероприятиям, которые внедряем в течение года. Рост производительности труда, оборачиваемость незавершенного производства в днях, считаем убытки от брака», – объясняет директор по производственной системе предприятия Александр Гусаров.
Сотрудники не планируют останавливаться на достигнутом.
«Продукт нового поколения – 530-й двигатель – состоялся. Теперь по нему есть отдельная программа каждодневного улучшения: на конвейере, на операциях в нашей зоне ответственности, и есть обширная работа с поставщиками, – говорит директор по развитию предприятия Николай Шамаль. – Мы локализовали на литейной площадке ГАЗа блок и головку. На своих площадях мы освоили производство кулачковых валов».

ЯМЗ как пример для подражания
Кайдзен стал не только частью производственной культуры предприятия, но и шагнул далеко за проходную. Большинство комплектующих для двигателей производятся внешними поставщиками, которые не входят в «Группу ГАЗ». Они также переняли ценный опыт коллег с Востока.
«На ЯМЗ создана группа аудита, которая по чек-листу проводит оценку каждого поставщика, – поясняет директор по производственной системе Александр Гусаров. – Мы показываем на примере ЯМЗ, как можно снизить производственные издержки и добиться снижения стоимости».
Примеру «Автодизеля» последовал ряд связанных с ним предприятий. Сегодня опробованные в Нижнем и Ярославле принципы используются на многих заводах страны.
Проведенные Олегом Дерипаской реформы привели ЯМЗ к завидным результатам. Производительность труда выросла в четыре раза. Завод прошел путь от выпуска двигателей ЕВРО-0 до разработки моторов ЕВРО-6 для Европы. Построена ультрасовременная производственная площадка, где делают двигатели ЯМЗ-530. Новый двигатель способен конкурировать как с Западом, так и с Китаем. А ведь страны, способные выпускать свой дизель, можно пересчитать по пальцам. Сегодня ярославские моторы устанавливаются на более чем 300 моделей техники.
Система, внедренная Олегом Дерипаской на ведущих предприятиях страны, распространилась не только в промышленности. На предприятия «Группы ГАЗ» ежегодно приезжают делегации из разных отраслей – финансовой, энергетической, строительной, сельского хозяйства. Специалисты берут на вооружение принципы, которые сделали заводы «Группы ГАЗ» современной и высокотехнологичной компанией XXI века.
Фото: Денис Круглов